In the era of Industry 4.0, the convergence of operational technology (OT) and information technology (IT) is reshaping the industrial landscape.
At the heart of transformation lies the critical need for seamless data flow from the shop floor to the cloud, enabling real-time insights and data-driven decision-making. This article explores how integrated machine visualization solutions, particularly the synergy between advanced Human-Machine Interface (HMI) software and rugged industrial hardware, are driving the next wave of innovation in smart manufacturing.
The Evolution of Industrial Automation: From Isolated Systems to Connected Ecosystems
Historically, industrial automation has faced several limitations:
- Data Silos: Isolated PLC systems and proprietary protocols hindered comprehensive data analysis.
- Limited Visibility: Lack of real-time, enterprise-wide operational insights impeded quick decision-making.
- Inflexibility: Rigid systems struggled to adapt to rapidly changing production requirements.
- Maintenance Complexities: Reactive maintenance approaches led to unexpected downtimes and increased costs.
- Skills Gap: As experienced operators retired, intuitive interfaces became crucial for maintaining productivity.
- Seamless connectivity across all levels of the industrial pyramid.
- Real-time data analytics for predictive maintenance and process optimization.
- Flexible and adaptive production systems.
- Enhanced cybersecurity to protect critical industrial assets.
- Improved operator efficiency through intuitive interfaces and augmented reality.
However, realizing these benefits requires a new approach to industrial automation—one that bridges the gap between OT and IT, from the edge to the cloud.
HMINavi stands at the forefront of HMI software innovation, offering a suite of features designed to facilitate the edge-to-cloud data journey:
1. Advanced Visualization Capabilities:
- Intuitive interface design with over 60 customizable application objects.
- Real-time process monitoring and control dashboards.
- Dynamic data representation through advanced charting, including historic radar charts.
2. Seamless PLC Integration and Data Acquisition:
- Support for over 500 PLC protocols, ensuring compatibility with a wide range of industrial equipment.
- Direct connectivity with PLCs for real-time data acquisition.
- Edge computing capabilities for local data processing and analysis.
3. Robust Data Management and Historization:
- Real-time data logging for comprehensive process analysis.
- Data historization and long-term storage solutions for trend analysis and compliance.
- Flexible recipe management for rapid production changeovers.
4. Cloud Connectivity and IoT Integration:
- MQTT protocol support for secure and efficient data transfer to the cloud.
- OPC UA server/client functionality for standardized data exchange.
- Integration with major cloud platforms, enabling advanced analytics and remote monitoring.
5. Enhanced Security Features:
- Multi-layered protection including project file encryption and granular user access control.
- Comprehensive audit trails for tracking system changes and user actions.
- Secure remote access capabilities for distributed operations management.
6. Scalability and Flexibility:
- Cross-platform compatibility, running on any x86 Windows system.
- Scalable architecture that grows with your business needs.
- Offline and online simulation modes for efficient HMI design and testing.
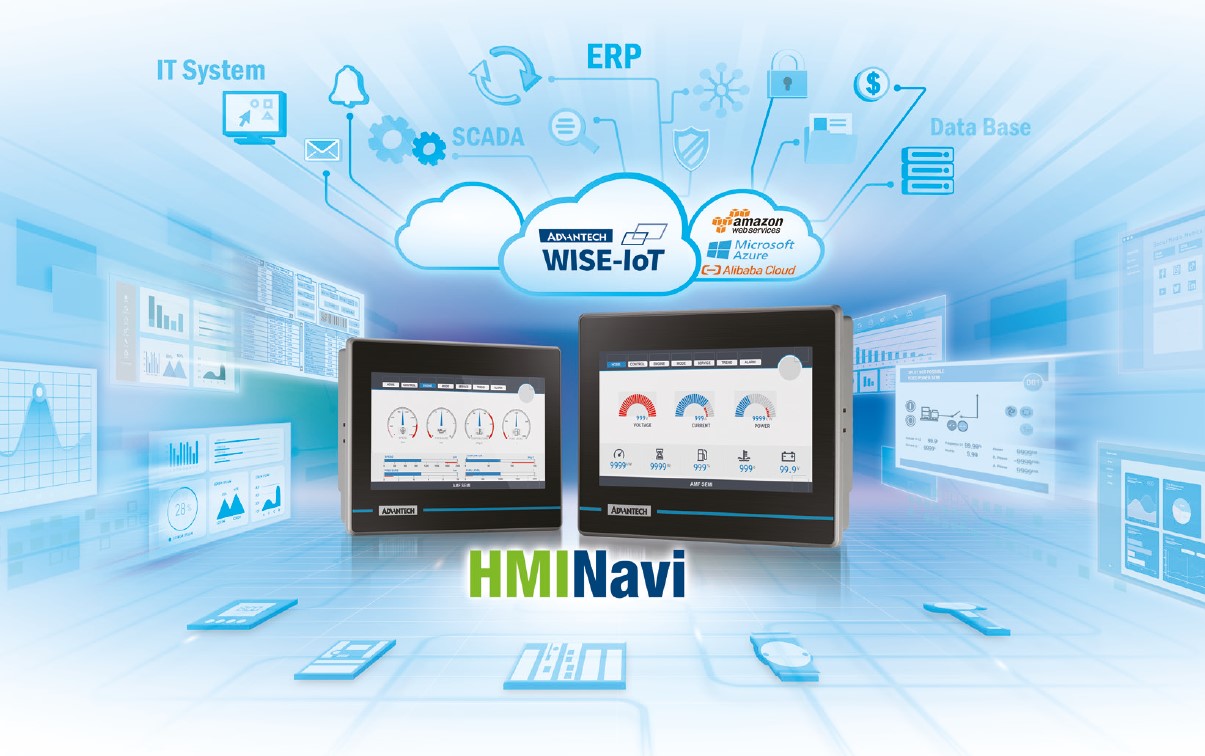
WOP-200 Series: Rugged Hardware for Reliable Edge Computing
The WOP-200 series operator panels provide the robust hardware foundation necessary for reliable edge computing and seamless cloud integration:
1. Environmental Resilience:
- Wide operating temperature range (-15°C to 65°C, extended to -25°C to 75°C in select models).
- IP66-rated front panel for superior protection against dust and water ingress.
- Vibration-resistant design for reliability in high-motion environments.
2. Enhanced Performance and Longevity:
- Powerful processors and ample memory for smooth operation of complex HMI applications and edge computing tasks.
- Conformal coating on motherboards, increasing lifecycle by up to 80%.
- High MTBF (Mean Time Between Failures) for reduced long-term maintenance costs.
3. Versatile Connectivity:
- Multiple serial ports (RS-232, RS-422/485) for legacy device integration.
- Dual LAN ports in select models for enhanced network flexibility and redundancy.
- Support for various industrial communication protocols.
4. Security-First Architecture:
- Real-Time Operating System (RTOS) for deterministic performance and reduced vulnerability to cyber threats.
- Isolated power input design for improved electrical noise immunity.
Transforming Industries Through Edge-to-Cloud Integration
The synergy between HMINavi and WOP-200 series enables a true edge-to-cloud solution, driving significant improvements across various industrial sectors:
Advanced Manufacturing
- Real-time visibility into production processes across multiple sites.
- Predictive maintenance strategies based on machine learning and AI algorithms.
- Flexible manufacturing capabilities, supporting quick changeovers and small-batch production.
Pharmaceutical Production
- End-to-end data traceability from raw materials to finished products.
- Compliance with FDA 21 CFR Part 11 and other regulatory requirements through secure data handling and audit trails.
- Real-time quality control and process optimization based on cloud-powered analytics.
Oil and Gas Operations
- Centralized monitoring and control of distributed assets, from wellheads to refineries.
- Predictive maintenance of critical equipment to prevent costly downtime.
- Enhanced safety through real-time risk assessment and rapid response to critical events.
Metal Fabrication
- Dynamic production scheduling based on real-time demand and resource availability.
- Automated quality control through integration of inspection data with cloud-based analytics.
- Energy optimization across the production line through comprehensive data analysis.
As industries worldwide grapple with the challenges of digital transformation, the need for integrated, edge-to-cloud solutions has never been more critical. Advantech's machine visualization solution, combining the versatility of HMINavi with the robustness of WOP-200 series panels, offers a clear pathway to this future.
By seamlessly connecting PLC data from the shop floor to the cloud, this integrated approach enables:
- Real-time decision-making based on comprehensive operational insights.
- Predictive maintenance strategies that minimize downtime and reduce costs.
- Flexible and adaptive production systems that respond quickly to market demands.
- Enhanced cybersecurity to protect critical industrial assets and data.
- Improved operator efficiency through intuitive interfaces and augmented reality support.
Whether you're looking to optimize existing operations, integrate diverse systems, or pave the way for a fully digitalized smart factory, Advantech's solution provides the tools and capabilities needed to succeed in today's competitive industrial landscape.
While the benefits of our integrated solution are clear, we believe that its true potential can only be fully appreciated through hands-on experience. We invite you to take the first step in transforming your industrial operations.
To learn about the available WOP-200 series products and their analogs, please click here